A manufatura enxuta é uma metodologia que se concentra em minimizar o desperdício nos sistemas de manufatura e, ao mesmo tempo, maximizar a produtividade. O desperdício é visto como qualquer coisa que os clientes não agreguem valor e não estão dispostos a pagar. Como benefícios, a manufatura enxuta pode incluir prazos de entrega reduzidos, custos operacionais reduzidos e melhor qualidade do produto.
Também conhecida como produção enxuta, ou enxuta, é uma prática que organizações de vários campos podem possibilitar. Algumas empresas em nível mundial que utilizam essa metodologia incluem Toyota, Intel, John Deere e Nike. A abordagem é baseada no Sistema Toyota de Produção e ainda é usada por essa empresa, assim como inúmeras outras. As empresas que utilizam um Sistema de Gestão Empresarial (ERP) também podem se beneficiar do uso de um sistema de produção enxuto.
A manufatura enxuta é baseada em uma série de princípios específicos, como o Kaizen, ou melhoria contínua.
Foi introduzida no mundo ocidental através da publicação de 1990 de “The Machine That Changed the World”, que foi baseada em um estudo do MIT sobre o futuro do automóvel detalhado pelo sistema de produção enxuta da Toyota. A partir dessa publicação, os princípios da manufatura enxuta passaram a influenciar profundamente os conceitos de produção em todo o mundo, bem como indústria fora da manufatura, como saúde, desenvolvimento de software e serviços.
Conheça os cinco princípios da manufatura enxuta
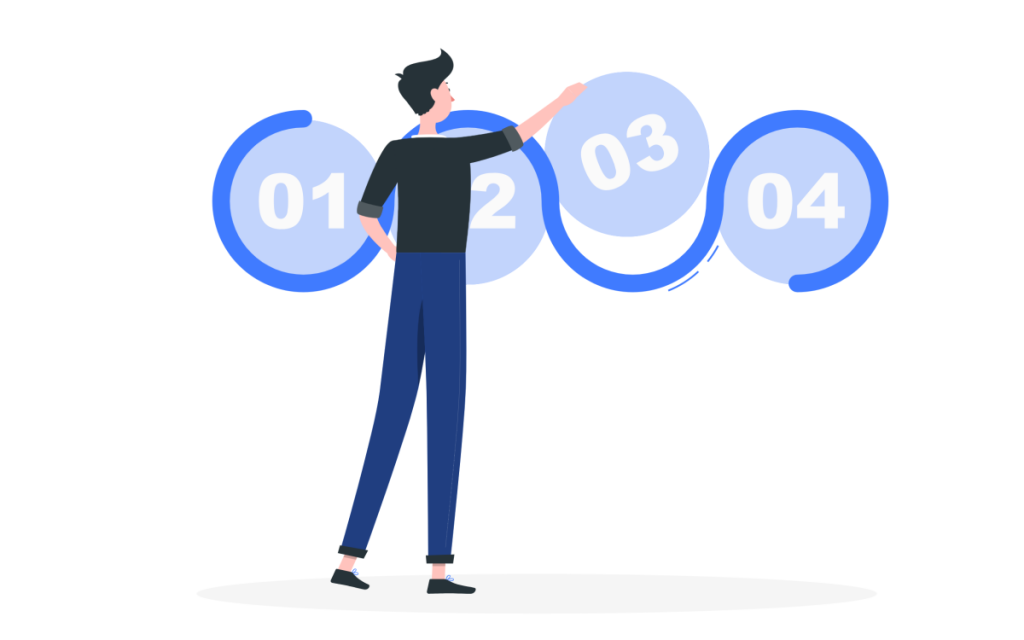
Os cinco princípios são Valor, Fluxo de Valor, Fluxo Contínuo, Produção Puxada e Melhoria Contínua e são usados como base para a implementação da metodologia.
1. Identifique o valor da perspectiva do cliente
O valor é criado pela empresa, mas é definido pelo cliente. As empresas precisam entender o valor que o cliente atribui a seus produtos e serviços, o que, por sua vez, pode ajudá-las a determinar quanto dinheiro o cliente está disposto a pagar.
A empresa deve se esforçar para eliminar desperdícios e custos de seus processos de negócios para que o preço ideal para o cliente possa ser alcançado – com o maior lucro para a empresa.
2. Mapeie o fluxo de valor
O objetivo é registrar e analisar o fluxo de informações ou materiais necessários para produzir um produto ou serviço específico com a intenção de identificar desperdícios e métodos de melhoria. O mapeamento do fluxo de valor abrange todo o ciclo de vida do produto, desde as matérias-primas até o descarte.
Deve-se examinar cada etapa do ciclo de resíduos. Tudo o que não agrega valor deve ser eliminado. O pensamento enxuto recomenda o alinhamento da cadeia de suprimentos como parte desse esforço.
3. Fluxo Contínuo
Elimine barreiras funcionais e identifique maneiras de melhorar o tempo de produção. Isso ajuda a garantir que os processos sejam tranquilos desde o recebimento do pedido até a entrega. O fluxo é fundamental para a eliminação de resíduos. A manufatura enxuta baseia-se na prevenção de interrupções no processo de produção e na viabilização de um conjunto harmonizado e integrado de processos em que as atividades se movem em um fluxo constante.
4. Estabeleça uma Produção Puxada
Isso significa que você só inicia um novo trabalho quando há demanda. A manufatura enxuta usa um sistema puxado em vez de um sistema empurrado.
Os sistemas de produção empurrada são usados no planejamento de recursos de manufatura (MRP). Com eles as necessidades de estoque são determinadas com antecedência e o produto é fabricado para atender a essa previsão. No entanto, as previsões geralmente são imprecisas, o que pode resultar em oscilações entre estoques demais e insuficientes, bem como cronogramas interrompidos subsequentes e mau atendimento ao cliente.
Em contraste com o MRP, a manufatura enxuta é baseada em um sistema puxado no qual nada é comprado ou feito até que haja demanda. Com a produção puxada, a empresa se torna mais eficiente e faz apenas o que será útil, evitando o surgimento de estoque e, depois, a necessidade de promoções ou descontos para acabar com ele.
5. Busque a perfeição com a melhoria contínua do processo
A manufatura enxuta baseia-se no conceito de buscar continuamente a perfeição, o que implica direcionar as causas-raiz dos problemas de qualidade e identificar e eliminar o desperdício em todo o fluxo de valor.
Os oito desperdícios da manufatura enxuta
O Sistema Toyota de Produção estabeleceu sete desperdícios, ou processos e recursos, que não agregam valor para o cliente. São eles:
- transporte desnecessário;
- inventário em excesso;
- movimentação desnecessária de pessoas, equipamentos ou máquinas;
- espera, sejam pessoas esperando ou equipamentos ociosos;
- superprodução de um produto;
- processamento excessivo ou dedicar mais tempo a um produto do que o cliente precisa, como projetos que exigem maquinário de alta tecnologia para recursos desnecessários; e
- defeitos, que exigem esforço e custo para correções.
Embora não tenha sido originalmente incluído no Sistema Toyota de Produção, muitos praticantes da manufatura enxuta apontam para um oitavo desperdício: desperdício de talento e engenhosidade não utilizados.
Sete ferramentas e conceitos de manufatura enxuta
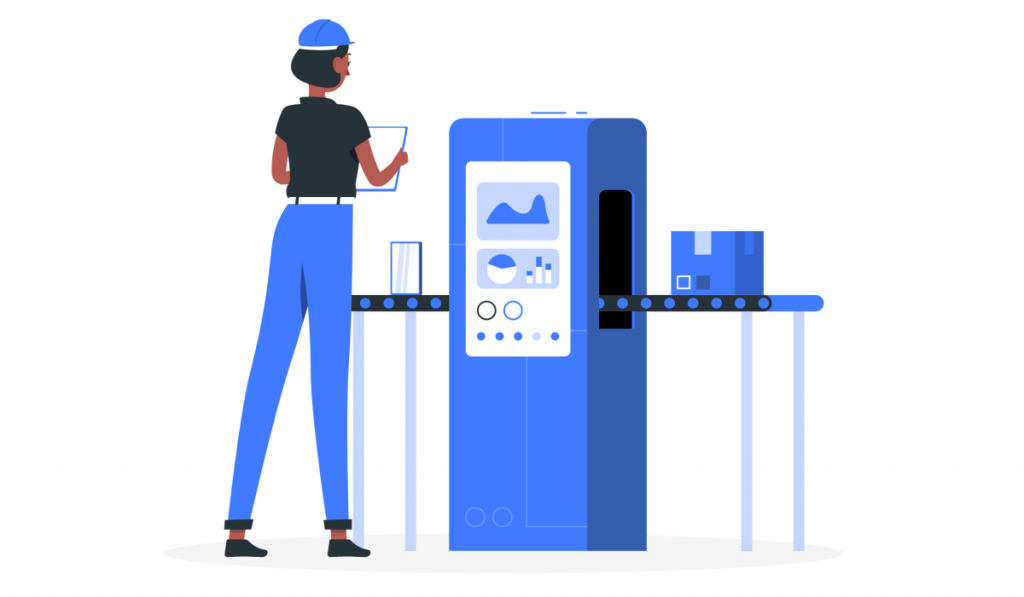
A manufatura enxuta exige uma busca incansável pela redução de tudo o que não agrega valor a um produto, ou seja, o desperdício. Isso torna a melhoria contínua, que está no centro da manufatura enxuta, uma obrigação.
Outros conceitos e processos importantes nos quais ela se baseia incluem:
Heijunka: nivelamento ou alisamento da produção que visa produzir um fluxo contínuo, liberando trabalho para a planta na taxa necessária e evitando interrupções.
5S: Um conjunto de práticas para organizar os espaços de trabalho para criar áreas eficientes, eficazes e seguras para os trabalhadores e que evitem o desperdício de tempo e esforço. O 5S enfatiza a organização e a limpeza.
Kanban: um sinal usado para agilizar processos e criar entregas just-in-time . Os sinais podem ser físicos, como uma etiqueta ou caixa vazia, ou enviados eletronicamente por meio de um sistema.
Jidoka: Um método que define um esboço para detectar uma anormalidade, parando o trabalho até que possa ser corrigido, resolvendo o problema e investigando a causa raiz.
Andon: Um auxílio visual, como uma luz intermitente, que alerta os trabalhadores sobre um problema.
Poka-yoke: Um mecanismo que protege contra erros humanos, como uma luz indicadora que acende se uma etapa necessária for perdida, um sinal dado quando um parafuso foi apertado o número correto de vezes ou um sistema que bloqueia uma próxima etapa até que todas as etapas anteriores são concluídas.Tempo de ciclo: quanto tempo leva para produzir uma peça ou concluir um processo.